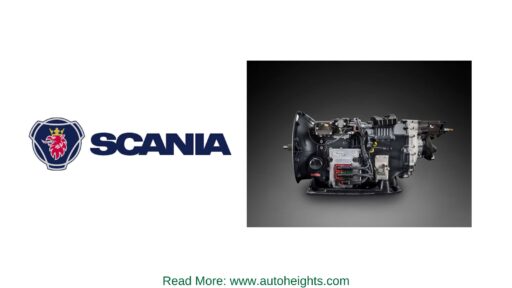
Scania has made automotive history by becoming the world’s first truck manufacturer to incorporate remanufactured components into its main assembly line in Sweden, marking a major leap towards sustainability in the heavy vehicle industry. The groundbreaking achievement came through Scania’s innovative Milestone gearbox remanufacturing project, which reduced material consumption by 50% and slashed carbon emissions by 45%, compared to producing new gearboxes. This is a pivotal demonstration that remanufactured components can seamlessly integrate into the production of new vehicles.
A Sustainable Breakthrough in Heavy Vehicle Manufacturing
Earlier this year, Scania, in collaboration with the KTH Royal Institute of Technology and Scandinavian Transmission Service AB, launched the iReGear research project. Funded by Vinnova, Sweden’s innovation agency, this initiative brought forth a gearbox that met the same rigorous standards and tests as new gearboxes. The remanufactured gearbox underwent thorough quality checks, matching the performance and durability expected from Scania vehicles.
A Game-Changer for the Automotive Industry
The gearbox met all functional requirements, proving to be “as good as new.” This project highlights the immense environmental benefits of remanufacturing, showcasing the potential to drastically cut resource consumption and emissions. In this case, the reuse of old parts reduced material usage by 50% and cut carbon emissions by 45%.
The Future of Remanufacturing and Circular Economy
While remanufacturing has traditionally been limited to producing spare parts for the aftermarket sector, accounting for only 1.1% of new production according to the European Remanufacturing Network, Scania’s bold move could shift the industry’s trajectory. Integrating remanufactured components directly into new vehicle production lines represents a significant step toward a circular economy, where sustainability meets efficiency without sacrificing quality.
Leading the Charge for Change
“This achievement is a shining example of how the heavy vehicle industry can adopt sustainable manufacturing practices without compromising on performance,” said Fredrik Nilzén, Head of Sustainability at Scania. He emphasized that this success sets the foundation for future manufacturing systems that consume fewer resources, produce lower emissions, and still deliver premium quality products.
Farazee Asif, Assistant Professor at KTH, added, “This project provides tangible evidence that circular manufacturing systems can integrate remanufacturing operations, leading to cost savings, environmental benefits, and uncompromised performance.”
Ola Stålebo, CEO of Scandinavian Transmission Service AB, reflected on the groundbreaking collaboration, stating, “After over 50 years of remanufacturing gearboxes, this project challenges the outdated perception that remanufactured parts are only for aftermarket purposes. This success proves that we’re on the verge of a new era where remanufacturing can be a key part of main production.”
The iReGear Project: A Step Towards a Cleaner Future
Running from September 2023 to May 2024, the iReGear project was spearheaded by KTH Royal Institute of Technology, with Scania and Scandinavian Transmission Service AB as key partners. Supported by Vinnova, this initiative underscores the importance of collaborative innovation in tackling resource scarcity and achieving climate goals.
As Scania leads the charge in sustainable automotive manufacturing, the success of the iReGear project opens the door for the wider adoption of remanufacturing practices across the industry, paving the way for a cleaner, more resource-efficient future in transportation.